Automotive Engine Design
It is an exciting time to be an automotive powertrain engineer, with many of the fundamental decisions that were made 50 or even 100 years being revisited, and many new options being explored thanks to the advent of new materials and advanced sensors and controls.
Fortunately, the ability to analytically evaluate candidate technologies and to fine-tune designs is keeping up with the need to explore new ideas.
A demonstration model is available to serve as a starting point for your explorations. While it is based on a four-stroke Otto cycle gasoline engine with 6 inline cylinders, the methods can be repurposed or extended to other cycles and configurations.
This FloCAD®-based model is built to explore short time scale events such as pressure waves within intake and exhaust runners, such that volumetric efficiencies and engine performance can be estimated. To do so, it models the transient actions of each of six cylinders independently through each stroke. Nonetheless, run times are fast enough (on the order of minutes) that parametric variations can be quickly explored. The focus of the problem is on the very short time‐scale events including pressure waves in the intake and exhaust runners. Details of flows, combustion, and heat transfer within the cylinder itself have been greatly simplified to preserve the focus on the air supply and exhaust systems.
Click here to download this sample from our support forum
This model was developed as a by‐product of an investigation of fast‐transient interactions within a turbocharged automotive engine.
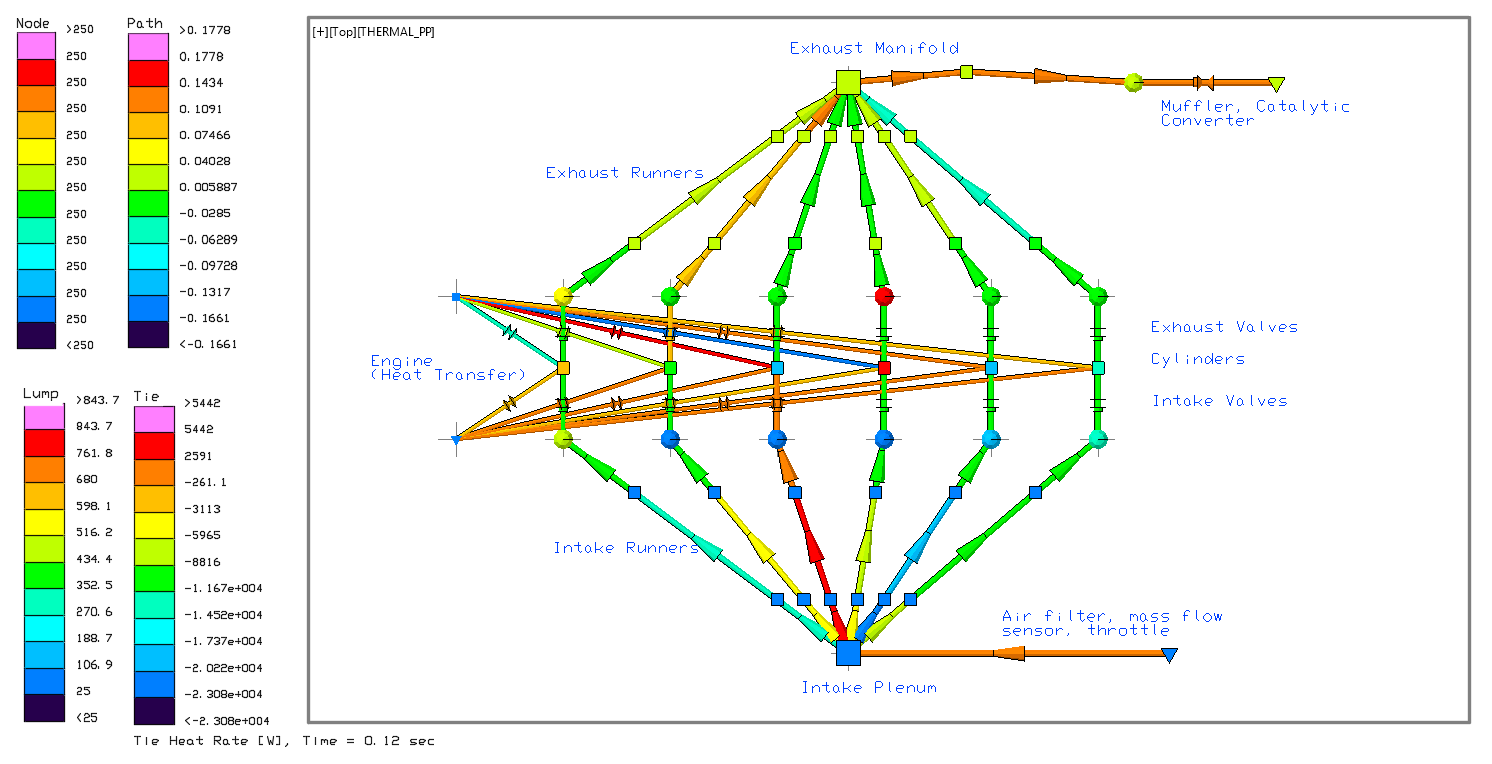
Postprocessed FloCAD® diagram (sketch-pad mode) showing temperatures and flows
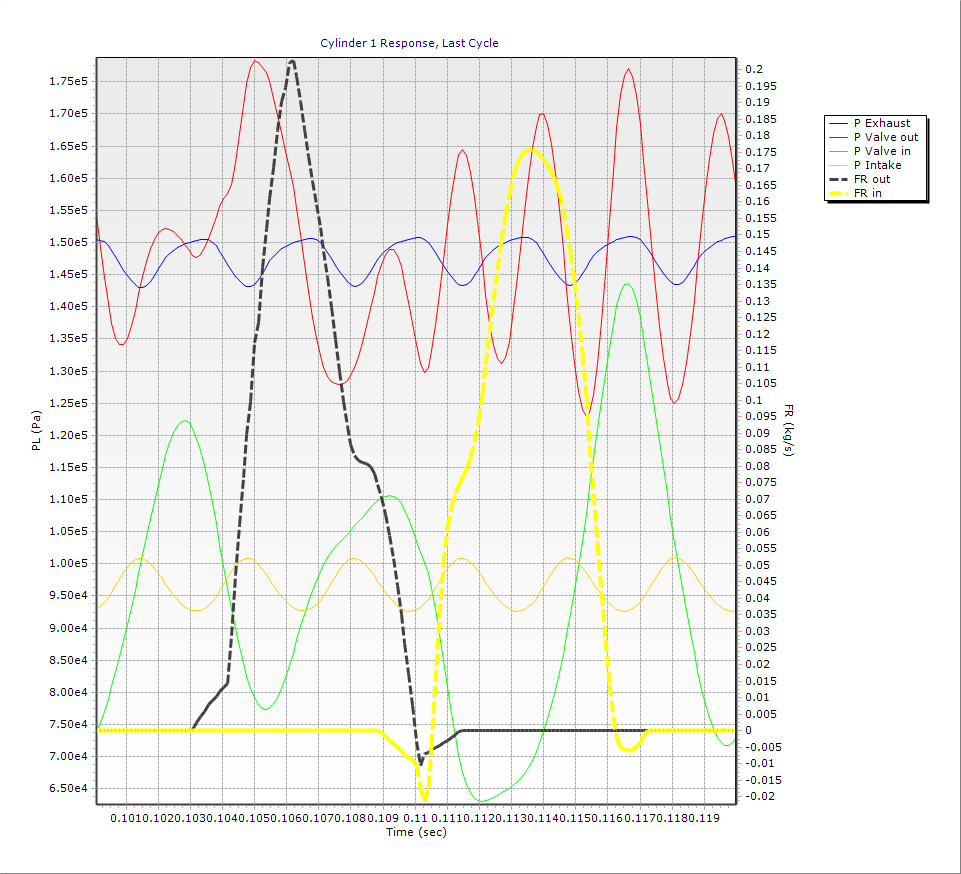