Integrated Design Analysis: Structural, Thermal, and Optical
STOP and Go
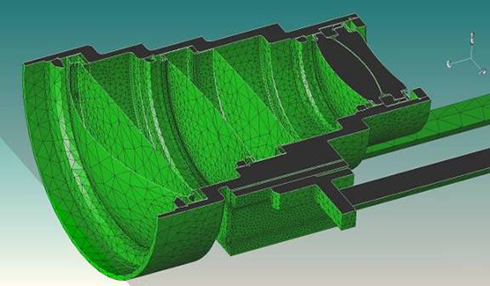
The answer is STOP: structural-thermal-optical integrated design analysis. Actually, this is not the answer so much as the goal, since many obstacles lie in the path of truly integrated design evaluation.
Many attempts have been made to achieve this goal. One early approach was to create a single design tool that could do a little optical analysis, a little structural analysis, and a little thermal analysis. “Little” meant that the unique aspects of each engineering discipline were ignored in order to create an all-in-one tool, where as those same aspects are the bread and butter of COTS (commercial off-the-shelf) tools targeted at each discipline. So while the all-in-one approach was useful for preliminary design by systems engineers, it could not be extended into later design phases where the skills of each discipline must be exploited, not oversimplified.
In the late 1990’s, CRTech led a NASA SBIR pathfinder project (“OptiOpt™”) that sought to overcome model translation hurdles between structural, thermal, and optical disciplines while respecting the unique talents and favorite tools of each engineering specialty. In addition to C&R’s Thermal Desktop®, Sigmadyne’s Sigfit® and ORA’s Code V® were therefore included in the software design. Significant successes were achieved, including the first automated STOP optimization using COTS tools (see publications: Integrated Analysis of Thermal/Structural/Optical Systems and Automated Multidisciplinary Optimization of a Space-based Telescope). Some very popular features of today’s Thermal Desktop, including automated mapping to independently-generated structural models and externally commanded parametric manipulations, were first developed as part of that project.
However, the OptiOpt project assumed that each discipline would start from the same CAD model, and then build independent models (the data from which must later be interchanged with other models). There was no centralization of model construction, and no attempt was made to capture the knowledge of each discipline such that it can be exposed to others on the design team. This meant that anything other than minor dimensional changes to the optical bench design had to be propagated manually by the team, and that the ability to intercommunicate design data also needed to be manually re-verified with each change.
A project by the Aerospace Corporation and Comet Solutions (now part of Aras) has made a significant advance in the ideal of integrated STOP analysis. While respecting the unique skills and tools of each discipline (significantly, the same ones used for OptiOpt: Thermal Desktop, Sigfit, and Code V), the Comet software also uniquely enables the ideal of that earlier “all-in-one” modeling environment: centralized model development.
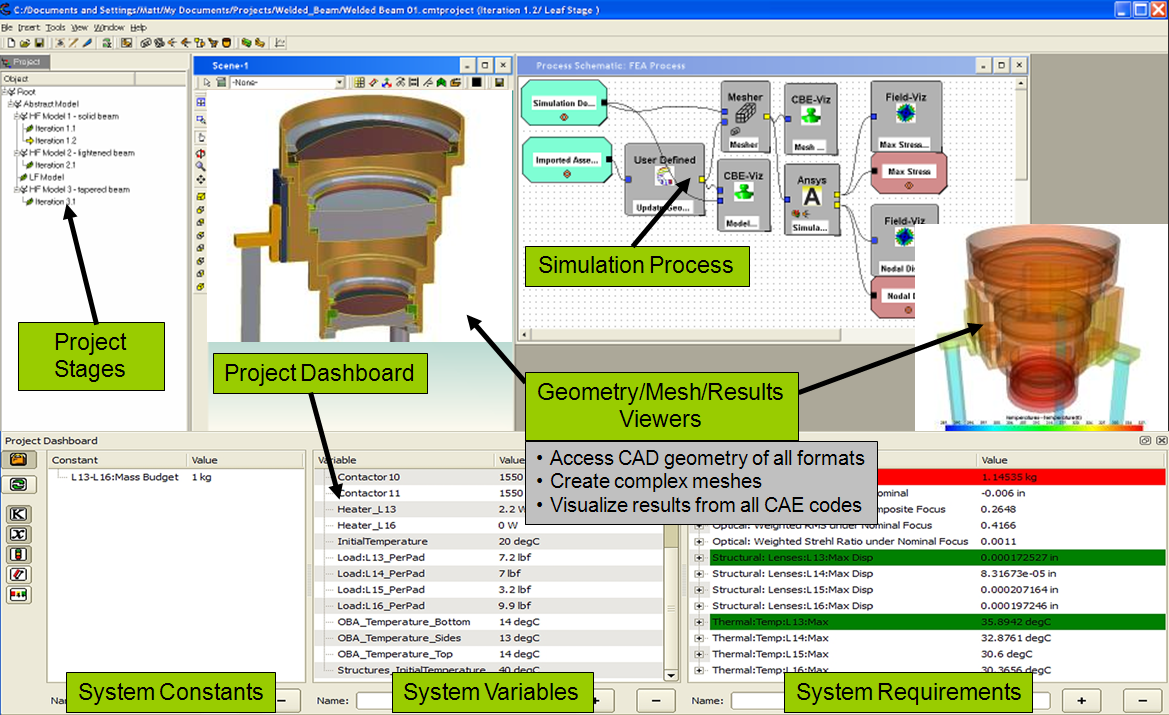
Aras Comet SPDM allows each discipline to participate in a common CAD environment, marking up a central drawing as needed to guide the generation of thermal, structural, and optical models. The experienced engineer's unique skills and tools are not lost or shoe-horned into a one-size-fits-all solution. Instead, the capturing of each disciplines’ methods into the central project means that design changes are readily accommodated. Team-level multidisciplinary design activities are thereby not only enabled, they are encouraged: each discipline can easily explore the ramifications that changes to their subsystem (e.g., materials selection, heater locations, strut sizing) have on the key mission objective: image quality.
The Aerospace team reported over two-fold increase in productivity, and good agreement between test and prediction.
Publications
- Integrated Analysis of Thermal/Structural/Optical Systems
- Automated Multidisciplinary Optimization of a Space-based Telescope
- "Collaborative design and analysis of Electro-Optical sensors", Jason Geis, Jeff Lang, Leslie Peterson, Francisco Roybal, David Thomas, The Aerospace Corporation
For More Information
- Aerospace Presentation: Concurrent Engineering Works: Thermal Results from an Integrated Structural Thermal Optical (STOP) Analysis Study
- Collaborative Design and Analysis of Electro-Optical Sensors Brochure
- Integration and APIs